Opening the Power of Welding WPS: Techniques for Performance and Safety And Security in Manufacture
In the realm of manufacture, Welding Treatment Requirements (WPS) stand as the foundation of welding operations, dictating the required steps for achieving both efficiency and safety and security in the manufacture procedure. Understanding the details of WPS is vital to harnessing its complete potential, yet many companies have a hard time to unlock truth power that exists within these papers (welding WPS). By delving into the approaches that optimize welding WPS, a globe of enhanced performance and increased safety awaits those going to explore the subtleties of this essential facet of construction

Significance of Welding WPS
The importance of Welding Treatment Specs (WPS) in the construction market can not be overemphasized. WPS offer as a crucial roadmap that outlines the essential steps to ensure welds are executed consistently and properly. By defining vital specifications such as welding procedures, materials, joint layouts, preheat temperature levels, interpass temperatures, filler steels, and post-weld warm therapy needs, WPS provide a standard method to welding that boosts effectiveness, quality, and security in fabrication procedures.
Adherence to WPS assists in achieving uniformity in weld quality, decreasing the chance of flaws or architectural failings. This standardization additionally assists in conformity with sector policies and codes, ensuring that produced frameworks meet the needed safety and security requirements. Additionally, WPS documentation enables welders to replicate successful welding procedures, bring about consistent results throughout various projects.
In significance, the precise advancement and strict adherence to Welding Treatment Requirements are paramount for maintaining the honesty of welded structures, protecting versus possible threats, and upholding the credibility of manufacture firms for delivering premium products and services.
Trick Aspects of Welding WPS
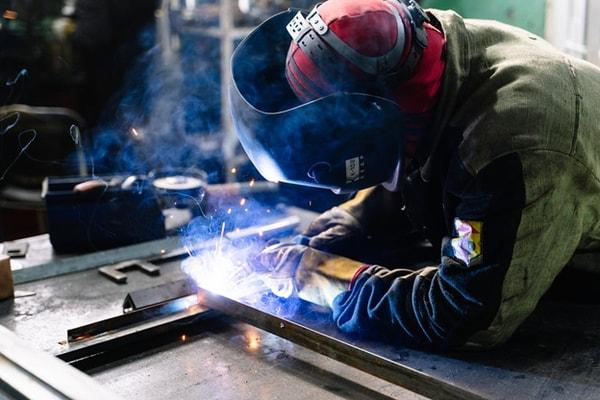
Enhancing Effectiveness With WPS
When maximizing welding procedures, leveraging the vital aspects outlined in Welding Procedure Specifications (WPS) becomes vital for making best use of and enhancing processes efficiency. One way to improve performance with WPS is by meticulously picking the ideal welding specifications. By sticking to the details standards supplied in the WPS, welders can make sure that the welding devices is set up correctly, leading to consistent and top notch welds. In addition, complying with the pre-approved welding series detailed in the WPS can considerably minimize the time websites invested in each weld, ultimately raising general performance.
Regularly examining and updating the WPS to incorporate any type of lessons learned or technical improvements can additionally contribute to performance enhancements in welding procedures. By accepting the standards set forth in the WPS and constantly looking for ways to maximize procedures, makers can achieve higher effectiveness degrees and superior end outcomes.
Ensuring Safety in Manufacture
Making sure safety in manufacture involves a multifaceted technique that encompasses numerous elements of the welding process. Welders must be outfitted with proper equipment such as safety helmets, handwear covers, and protective apparel to alleviate dangers linked with welding tasks.
Furthermore, adherence to correct ventilation and fume extraction systems is critical in preserving a healthy and balanced work setting. Welding fumes include unsafe compounds that, if inhaled, can posture severe health threats. Executing reliable ventilation procedures helps to lessen exposure to these harmful fumes, promoting breathing health and wellness amongst workers.
Regular equipment upkeep and evaluations are additionally vital for ensuring security in fabrication. Malfunctioning machinery can result in mishaps and injuries, underscoring the importance of prompt repair work and routine checks. By focusing on safety and security measures and cultivating a culture of awareness, construction facilities can create a effective and safe and secure job environment for their personnel.
Executing WPS Finest Practices
To improve functional performance and ensure quality results in fabrication procedures, incorporating Welding Procedure Requirements (WPS) finest methods is paramount. Selecting the suitable welding procedure, filler product, and preheat temperature specified in the WPS is important for accomplishing the check this wanted weld quality. Making sure that certified welders with the required qualifications carry out the welding procedures according to the WPS standards is vital for uniformity and integrity.
Conclusion
Finally, welding WPS plays a crucial duty in ensuring efficiency and security in construction procedures. By concentrating on crucial elements, boosting performance, and implementing best practices, firms can maximize their welding operations. It is vital to focus on precaution to stop mishaps and make certain a smooth production process. By following these techniques, businesses can open the complete capacity of welding WPS in their manufacture procedures.
In useful link the realm of fabrication, Welding Treatment Specifications (WPS) stand as the foundation of welding procedures, determining the needed actions for accomplishing both efficiency and safety in the fabrication process. By specifying crucial criteria such as welding procedures, materials, joint designs, preheat temperatures, interpass temperature levels, filler steels, and post-weld warm treatment needs, WPS offer a standard method to welding that improves efficiency, top quality, and safety and security in manufacture procedures.
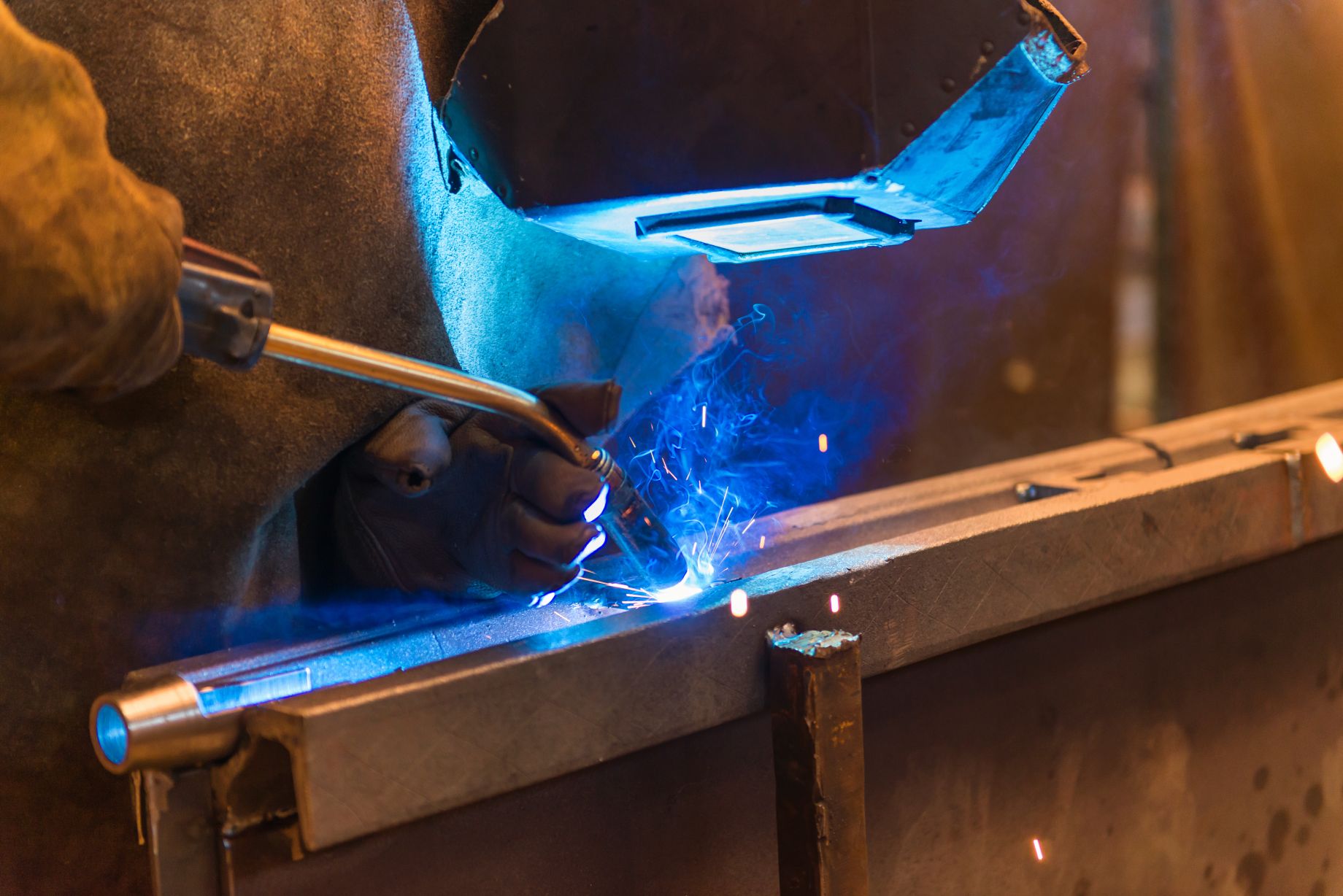
When optimizing welding operations, leveraging the crucial elements described in Welding Treatment Specifications (WPS) becomes vital for simplifying procedures and taking full advantage of efficiency. (welding WPS)